1940-1969年
1958年 日本初の水道用伸縮管ベローズ開発(旧横浜工場)
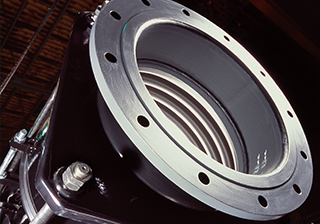
水道配管において、よりシール性能に優れた当社ベローズ型伸縮管継手が東京都水道局に採用され、以後、全国各地の水道局に普及した。
1995年の阪神・淡路大震災後、地震や地盤沈下によるパイプの損傷を軽減する継手として改めて注目を集め、現在ではライフラインの確保に欠かせない存在となっている。
1995年の阪神・淡路大震災後、地震や地盤沈下によるパイプの損傷を軽減する継手として改めて注目を集め、現在ではライフラインの確保に欠かせない存在となっている。
1970-1989年
1974年 世界最大の地熱発電用伸縮管を納入(旧横浜工場)
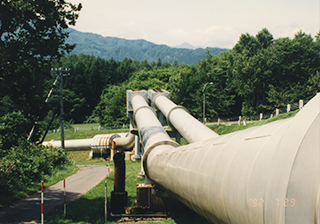
世界的なエネルギー需要の伸びに伴う原油高の影響から発展途上国においては、地熱発電所の建設が盛んに行われるようになった。
当社においてもコスタリカで世界最大の地熱発電用伸縮管を受注。この伸縮管は外径がФ3200と大きいため、ベローズ溶接時のひずみ除去や、完成時の搬送方法などに苦労を要したが現在も現役で活躍している。
当社においてもコスタリカで世界最大の地熱発電用伸縮管を受注。この伸縮管は外径がФ3200と大きいため、ベローズ溶接時のひずみ除去や、完成時の搬送方法などに苦労を要したが現在も現役で活躍している。
1978年 JT60真空容器用タマゴ型ベローズを開発(新潟工場)
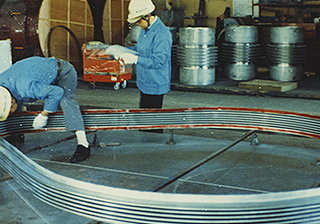
核融合実験用真空装置に用いられるタマゴ型ベローズ開発の依頼を受け、日本金属工業との共同研究により超真空状態に耐える材料選定、超音波検査による材料管理、エックス線検査による溶接管理を実施するなど、安全性を確保するための品質管理体制を構築。
これを機に原子力発電の重要配管に使用する伸縮管継手は、ほとんどのシェアを当社が占めるようになった。
1981年 日本初のLNG複合サイクル発電用伸縮管継手を製作(旧横浜工場)
LNG複合サイクル発電とは、圧縮した空気と燃料のLNG(液化天然ガス)を燃焼させ、ガスタービンで発電した後、その排熱を利用した蒸気タービンでも発電する2段構えの熱効率が高い発電方式のこと。
しかし、内部を腐食性の強いコンバインド(複合)ガスが通るため、耐食性能が求められる。
しかし、内部を腐食性の強いコンバインド(複合)ガスが通るため、耐食性能が求められる。
1984年 屋内配管 ガス用フレキシブル管製作開始(神林工場)
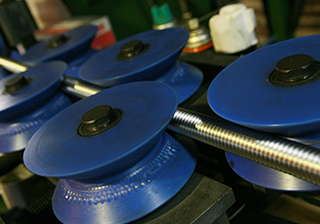
ガス配管用フレキ管の製造において、当社は後発メーカーであったが、取り付け金具との機密性を高め、コストダウンを図ったワンピッチチューブの開発により、国内シェアを30%に伸ばした。
1990-1999年
1992年 H-1ロケット(9号)用高圧用伸縮管継手を納入(新潟工場)
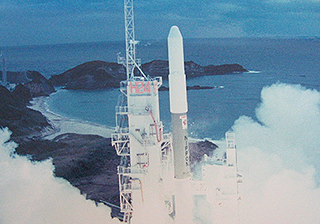
人工衛星打上げ用として、当時の宇宙開発事業団(NASDA)が開発、実用化したH-1ロケット(9号)の国産第2段エンジンへの液化酸素供給配管に当社の伸縮管継手が採用された。液体酸素の流体条件(低温(マイナス196℃)、高圧(25MPa))を満たすための製品仕様となっている。
1992年 世界最大級のブレイドマシンを設置(熊本工場)
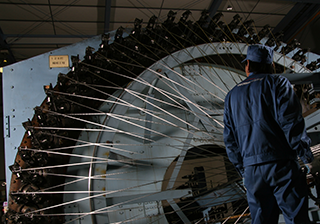
フレキシブルホースの耐圧性能は、外層に被覆されるステンレス製のブレイドによって確保される。従来の大口径製品には、帯状のブレイドが装着されていたが、これは柔軟性がなく、また長尺製品への編組が困難なため、製品全長に制限があった。これに代わり線状のブレイドが装着可能な大口径用ブレードマシンを設置。Ф600mmまでの製品に柔らかい線状ブレイドの編み付けが可能となった。
1993年 真空バッチ式大型熱処理炉を設置(熊本工場)
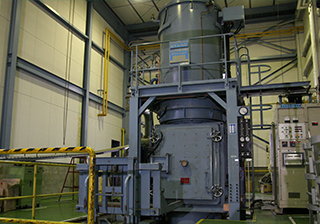
金属製フレキは、材料であるステンレスの耐熱性能、耐腐食性能の向上を目的として、金属組織の変化を再生するため1050℃で熱処理を行う。当社は、この工程を従来のトンネル式連続炉から真空バッチ炉へ切り替え、大幅なコスト削減、品質の安定性を確保することに成功した。また、20メートルを超える長尺完成品の状態での熱処理も可能で、これは同業他社にはない独自の設備となっている。
1993年 加圧送水装置用フレキシブル継手の消防法認定第1号(熊本工場)
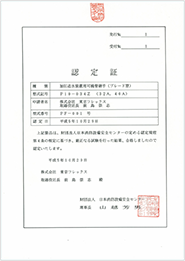
消防法第17条第1項の規定に基づく消防用ポンプを用いる加圧送水装置の吸込側および吐出側配管に使用するフレキシブル継手の性能が基準化された。
当社は第1号として承認され、過酷な環境においても品質、および安全性に何ら支障がないことを証明した。
当社は第1号として承認され、過酷な環境においても品質、および安全性に何ら支障がないことを証明した。
1994年 業界初、金属製大口径(350A)製鉄用フレキシブル継手を製作(熊本工場)
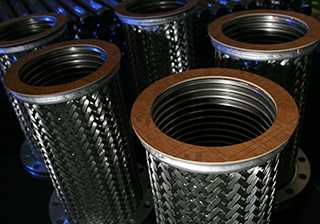
製鉄転炉設備における酸素供給配管の接続可動部には、これまでゴム製のホースが使用されていたが、製作可能な口径に制限があったり、耐温度性能が金属製と比べ劣るという問題があった。ここに当社の金属製フレキシブル継手が採用されたことで、可動部の劣化や流量の問題が解決し、製鉄所の生産効率の向上に貢献した。
1998年 ウォールジョイントを開発(新潟工場)
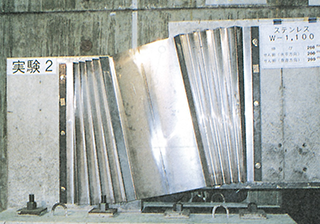
1995年の阪神・淡路大震災では、多くのLPG基地等でタンク周囲の防油(液)提が破損し、機能しなくなってしまったが、ウォールジョイントは、地震時の液状化等の状況においても防油堤からの油漏れを防いだ。
これを機に消防危32号「防油堤の漏洩防止措置等について」ならびに消防危33号「防油堤目地部の補強材の性能等について」によって、防油堤目地部の可撓性材に関する技術上の指針が通知されることになった。これにより、目地部の補強材の試験確認に係る業務規定およびその実施細目が決まり、当社のウォールジョイントは改めて高い評価を得ている。
これを機に消防危32号「防油堤の漏洩防止措置等について」ならびに消防危33号「防油堤目地部の補強材の性能等について」によって、防油堤目地部の可撓性材に関する技術上の指針が通知されることになった。これにより、目地部の補強材の試験確認に係る業務規定およびその実施細目が決まり、当社のウォールジョイントは改めて高い評価を得ている。
1999年 自社内にクリーンルーム(クラス100、1000、10000)を保有
ガス成分分析計(ガスクロ)設置(熊本工場)
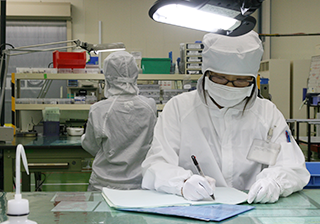
半導体の製造には、空気中に含まれる微細なごみ(パーティクル)が製品の良否に影響を及ぼすため、当社が製造する半導体製造装置部品の製造時においてもクリーンな環境をつくる必要があった。
当社においては最も清浄なクラスに属する100から1000、10000の3種のクリーンルームを設置し用途によって使い分けている。
当社においては最も清浄なクラスに属する100から1000、10000の3種のクリーンルームを設置し用途によって使い分けている。
2000-2009年
2001年 材料分析装置を導入(新潟工場)
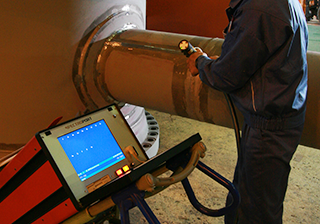
フレキシブルホースや伸縮管継手の主材料であるステンレスは、中に含まれるニッケル、クロム、鉄などの成分量によって種類が異なり、腐食性などの性能も変わる。当社では、顧客の要望に応じ原料となるステンレスコイルの入荷時において、鉄鋼メーカーからの成分分析表であるミルシートをチェックするのと同時に、独自に材料分析装置を用いたチェックを行い、製品の品質の安定性に努めている。
2003年 FC(水素燃料)自動車用フレキシブルメタルホースを開発
FC自動車の燃料電池へ水素を供給するラインの振動吸収用として、1999年の試験開発段階から参画。自動車業界への製品納入は初めての経験であったが、2002年末の納入を目標に、さまざまな試験項目、性能要求をクリアしていきながら顧客とともに開発を進めた。
2003年 電気事業法認証取得(新潟工場)
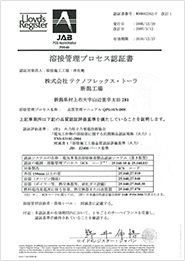
2003年8月1付で発電設備の安全管理審査実施要領の改正が行われ、当該審査のなかの溶接安全管理検査の実施に関する民間製品認証制度が導入された。火力発電所向けの製品を手がける当社もいち早くこの認証を取得し、これまで以上のサービスの提供を目指すこととなった。
2005年 新構造・非溶接型フレキシブルメタルホースF118を開発・販売
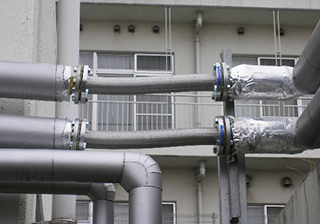
国土交通省/諸官庁仕様に対応したポンプ防振継手を新たに開発・販売。従来型はコストダウンの限界に達していたため、設計・開発時から全面的な見直しを図った。外層ブレイドの取り付け方法や、広範囲な用途に対応できるようパッキン面を大きく仕上げるなど、コストを意識した弊社独自の新しい構造を採っている。
2007年 新構造・非溶接型消火用フレキシブルメタルホースF138を開発・販売
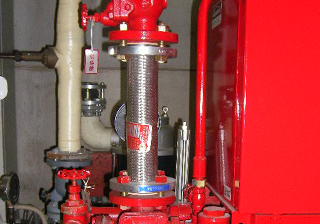
2005年に発売したF118と同様の見直しを図った建築設備用消火配管の消火ポンプ防振継手F138の開発・販売を開始した。
2009年 SDF工法 ドラムフレキの開発・販売
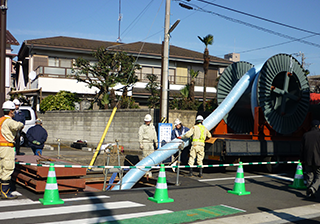
SDF工法とは老朽化した給水本管の改修として、従来の既設管内挿入工法では施工が困難な、曲がり部を含む配管にステンレス・フレキ管を引き込み、管路更新工事を行なう新たな工法。
軌道下や河川下の伏せ越し配管、交通量の多い道路横断、他企業の埋設物が輻輳している場所など、開削が困難な場所に敷設された既設管の更新に大変有効な工法であるとの評価を得ている。
軌道下や河川下の伏せ越し配管、交通量の多い道路横断、他企業の埋設物が輻輳している場所など、開削が困難な場所に敷設された既設管の更新に大変有効な工法であるとの評価を得ている。
2010-2019年
2010年 アルミ複合ポリエチレン管の生産に取り組む
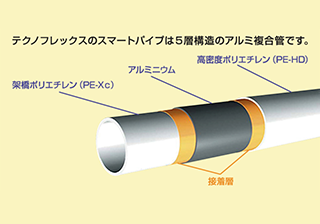
会社設立以来、ステンレス製フレキシブルホース、ベローズ伸縮管継手を専門に生産していたが、市場の変化に追従すべく樹脂製材料のホースの生産に取組みを始める。アルミ複合ポリエチレン管はアルミニウムがポリエチレン樹脂にサンドイッチされた多層構造の樹脂管で、欧州、中東及びアジア地区で広く普及しており既存の樹脂管に生じる”酸素透過”という大きな問題点を改良したパイプ。今後の普及が期待される。
2012年 400Aオメガチューブの開発
SDF工法の要求に応えるべく、呼び径400Aのオメガ成型チューブとブレイドを新たに開発した。
2013年 アルミ複合ポリエチレン管製スプリンクラーホース スマートSPを開発
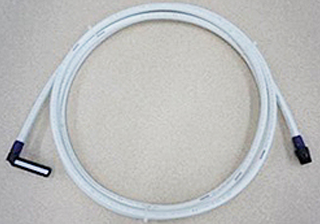
既存の鋼管と金属製巻き出しフレキの組合せによるスプリンクラー巻き出し工法に代わる新たな配管工法として、アルミ複合ポリエチレン管を本体としたスプリンクラー巻き出しホース/スマートSPの開発を開始。
2014年 ASME NPT 取得
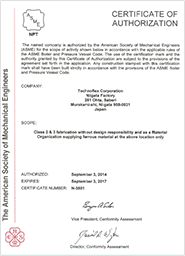
当社は、国内原子力発電所向け重要配管に用いられる伸縮管継手を殆どのシェアで受注・生産している。そして、更に世界市場への展開を視野に、原子力発電が加速したフクシマの事故以前に、国際的な規格認証の標準となりつつあるASME-NPT取得を目指し、プロジェクトチームを発足させ、その取得に取り組んできた。その結果、2014年9月ASME-NPTスタンプを取得することが出来た。
伸縮管継手メーカーにおいて、当スタンプを取得している企業は、世界に数社のみで、アジアの伸縮管継手メーカーとしては初めての取得となる。
強力な品質保証能力の保持の証となる、このASME-NPTスタンプを元に、高信頼性・高品質の伸縮管継手を以って、世界に貢献して行きたい。
伸縮管継手メーカーにおいて、当スタンプを取得している企業は、世界に数社のみで、アジアの伸縮管継手メーカーとしては初めての取得となる。
強力な品質保証能力の保持の証となる、このASME-NPTスタンプを元に、高信頼性・高品質の伸縮管継手を以って、世界に貢献して行きたい。
2015年 UL, FM 認証スプリンクラーフレキの開発/取得
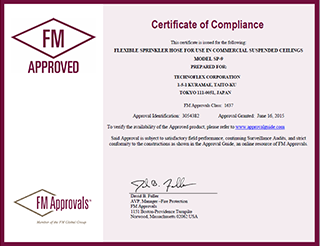
世界のスプリンクラー市場に挑戦すべく米国の保険期間が定めるスプリンクラーフレキの開発、認定取得を開始。着手から3年の期間を得てUL規格、FM規格の認定取得を実現した。
2015年 SDFフレキ 500Aの開発
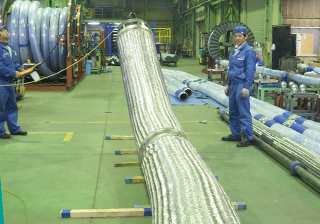
SDF工法における唯一のデメリットが挿入管による配管の縮径で、これは給水量の減少に繋がる。できるだけ大きな挿入管の開発が求められ、400Aフレキを遥かに超える呼び径500Aの開発を行なった。
2017年 SDF工法 第1回インフラメンテナンス大賞を受賞
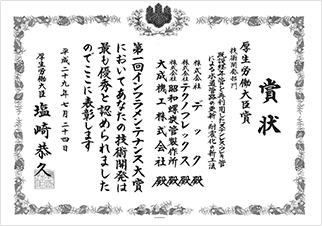
SDF工法が優れた耐震化の新工法として認められ、第1回インフラメンテナンス大賞 厚生労働大臣賞を受賞した。